All our textiles - traditionally known as ‘Tais’ (ti-esh) - are woven on back-strap looms.
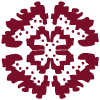
The tradition of Tais weaving in Timor-Leste
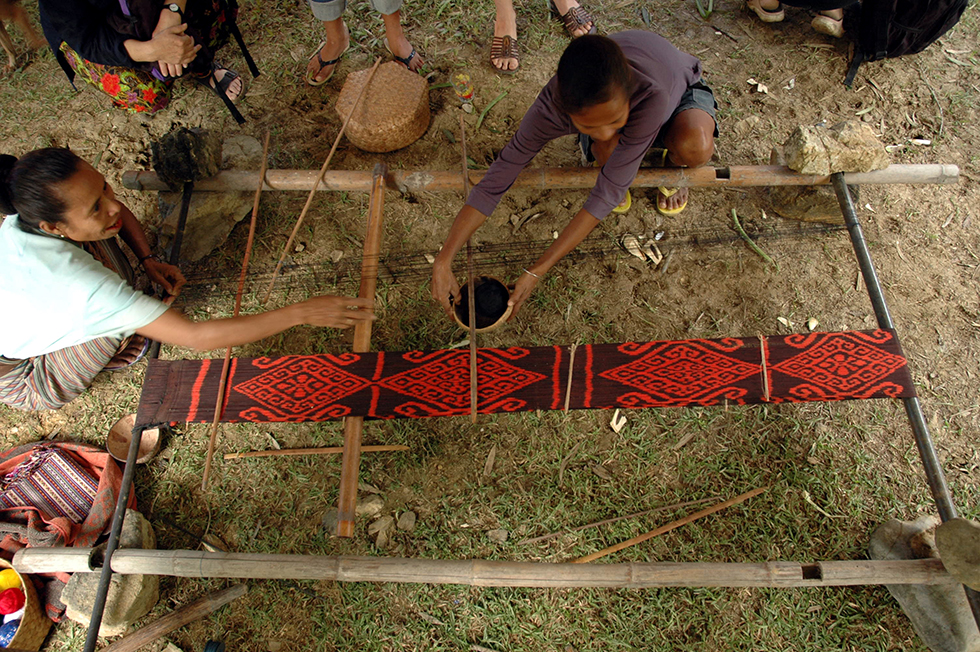
Threads of hope
Tais, the traditional cloth of East Timor, is the central thread that weaves the friendship between ETWA and East Timorese women. Through the medium of Tais, women have the chance to improve their quality of life and uphold the customs and traditions that shape East Timorese identity. By applying skills that are steeped in the old ways, women weave new opportunities and culture and commerce merge for development. Unlike in the west where generally little importance is placed on women’s work with textiles, in East Timorese culture, cloth plays a key role in social and ritual life and also in assigning women’s standing in communities.
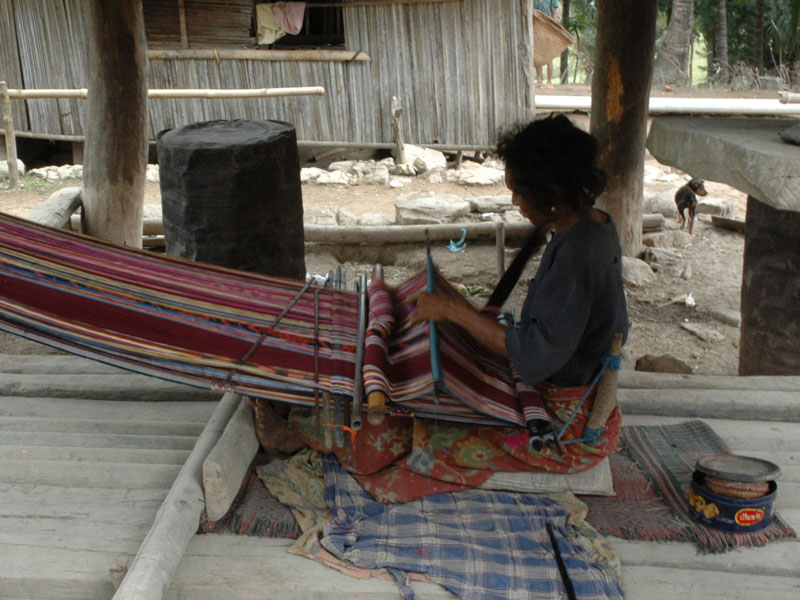
Weaving Women's place
Tais embody women’s contribution to cultural and social life in East Timor. They clothe communities and play a central role in rituals to celebrate birth; honour the dead and in particular, in the traditional rite of marriage.
Purposefully and carefully woven matrimonial sets, consisting predominantly of a Tais Feto (women’s Tais) and Tais Mane (man’s Tais), are the weavers’ exclusive gifts; symbolic of the coming together of two communities or the broader social contracts that are bound up in the unity of marriage. Strong affiliations to clan and to place are influential notions in Timorese culture, and are demonstrated in the practical and symbolic functions, and aesthetic aspects of Tais.
Weaving brings families together. Young girl pictured here helping her aunty wind the warp. Like Scottish kilts, Tais signify clan and ancestral heritage. Motifs and colour combinations are identifiers of ethnic groups and as the weavers of the cloth; women are the carriers of a cultural language that reflects the birth place of whole communities. Through Tais, this cultural language is expressed and weavers’ play a collective role in maintaining place-based identity.
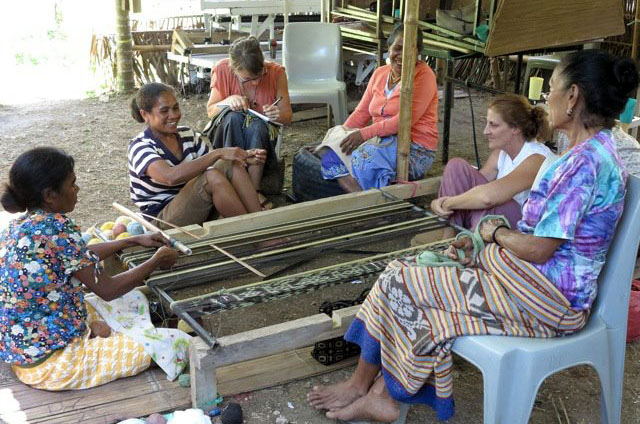
Social Process
Weaving also provides spaces for individual and communal expression and creativity. The weaving process is a social process; undertaken communally with often four generations of women involved. Techniques are passed through generations and girls as young as four years old are taught to weave by their mothers, grandmothers, sisters and aunties. The whole process fosters and strengthens intergenerational relationships and processes of cooperation between genders. Although principally considered women’s work, men are often seen assisting women in both growing and dying cotton and assembling the looms.
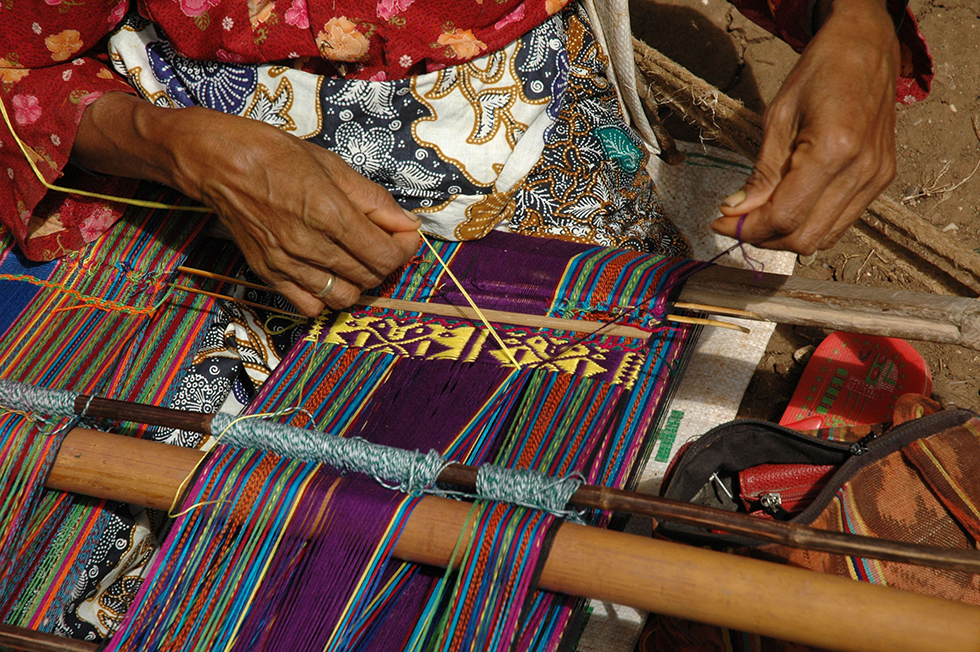
Historical Documents
The island of Timor comprises a rich blend of peoples and cultures, each with distinct customs and textile designs. The Portuguese influence is obvious in the remote eastern regions of Iliomar where Tais feature traditional motifs integrated with colourful stripes and bands of small flowers of European inspiration. In the central highlands, mono-coloured, black Tais with subtle geometric strips contrast the bold, Dutch inspired floral designs of the western region. Through the art of Tais, a woven narration of East Timor’s cosmology and history has been recorded. They weave a discourse that reflects spiritual beliefs, ethic fusion, diversity and colonial transformations.
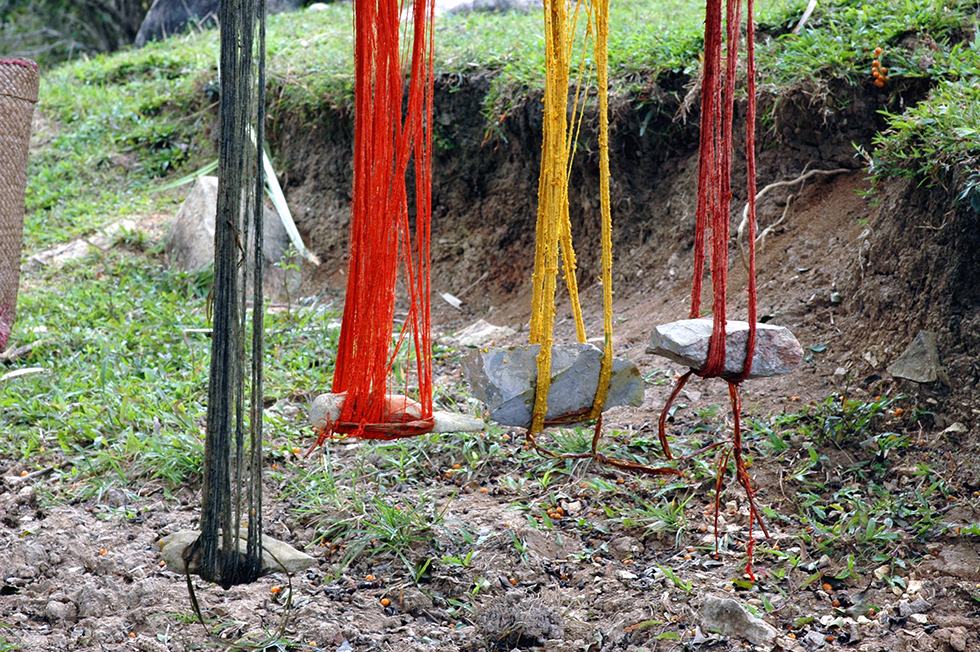
Symbolic Colours
The main fibre used for weaving is cotton, which is hand-spun and dyed using natural pigments obtained from local leaves, bark, ash and clay. Red is often the prevailing colour. For many Timorese communities, red is associated to new and lasting life, sacrifice and courage, as is seen by the symbolic colours of the Timorese Flag which are red for the liberation struggle; black for triumph, yellow for colonial remnants and the white star is the light of peace.
The Weaving Process
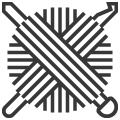
Prepare the Cotton
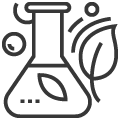
Dye the Cotton
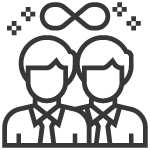
Wind the Warp
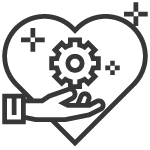
Weave the Weft
Prepare the Cotton
The first step to making Tais starts with raw cotton on the vine known as ‘kabas’. Before cotton can be spun into yarn, the raw fibres are separated from the seeds in a process known as ginning. The cotton is then hand spun and wound into balls prior to dying or weaving. Today, commercial cotton is combined with traditional designs to create contemporary Tais that maintain their customary elements.Dye the Cotton
Dying the cotton is the next step. All weavers have their secret recipes to create desired tones and a good dyer is seen to be similar to a medieval alchemist. Colours are specific to local areas and the plant life. Bark, roots, soil, mango skin and leaf of potato, cactus flowers and turmeric are but a few of the organic materials used to create the vibrant colours of traditional Tais.Wind the Warp
Two sets of threads, the warp or vertical threads and the weft or horizontal threads are interlaced during the weaving process to create the cloth. The weaver needs help to wind the first lot of threads known as the warp (vertical threads). Balls of cotton are placed inside coconut shell dishes, passed back and forth and wound n precision around a simple warping frame. The warp threads are then transferred to the loom and the weaving process begins.Weave the Weft
The warp is attached to a strap which hugs the weavers’ lower back, hence the name ‘back-strap loom’. With the warp stretched out in front of her, the weaver maintains the tension on the cloth by leaning back and keeping her legs straight and extended during the weaving process. The pressure on her legs and lower back creates intense pain if the weaver sits at the loom for too long. As the women we work with are poor in a monetary sense, the looms can be assembled using local timbers, often at no cost.Hand Woven
LO’UD Cooperative members use simple back-strap looms, which are often fashioned with timber off-cuts, old twine and rice sacks. Each weaver has a small selection of cherished tools - like honed mortar and pestles and beaters - often handed down through generations. LO’UD women have highly developed skills of artisanship and creativity. Their participation in LO’UD elevates their status in their communities and firmly places weaving as legitimate cultural and economic activity, valuable to their day-to-day life. Importantly they join together as women, which as we know is beneficial to maintaining mental health.
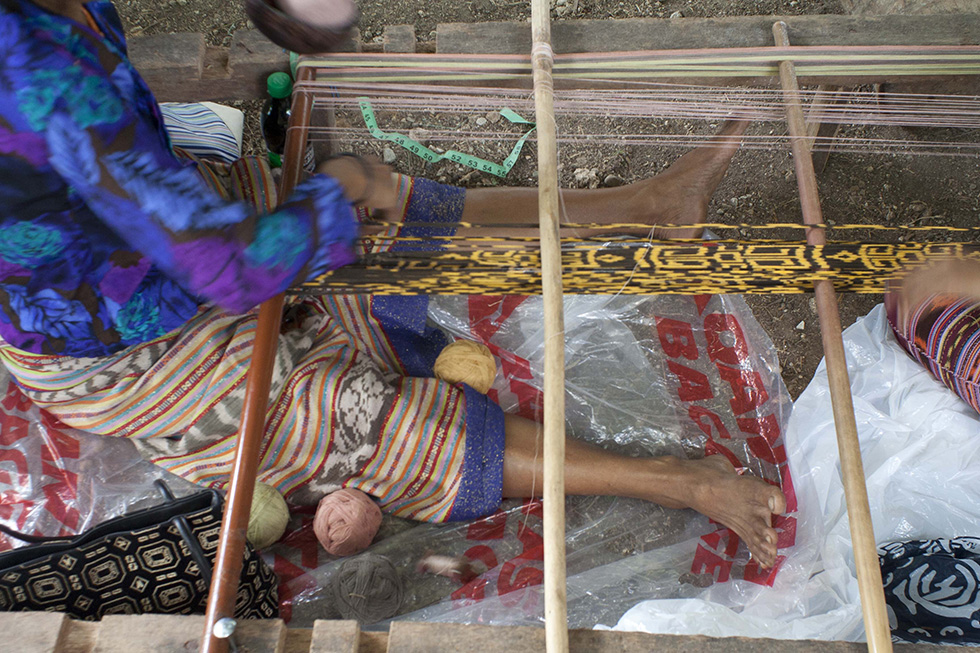
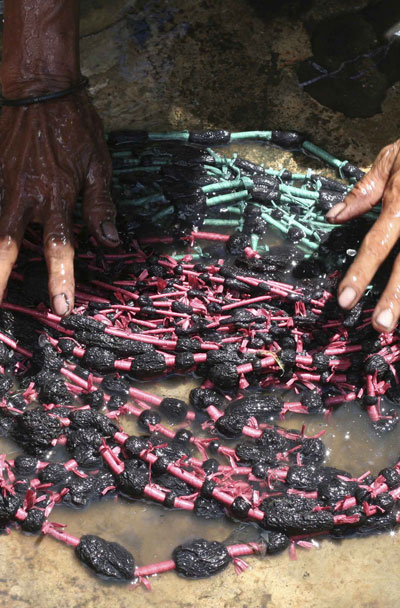
Futus
Futus is the meticulous process of creating designs by tying to form specific patterns before the yarn is dyed. The tied warp threads are immersed into dye mixtures, cooled and immersed again depending on the number of colours to be combined. Weavers who produce quality Futus are considered highly intelligent and gifted.
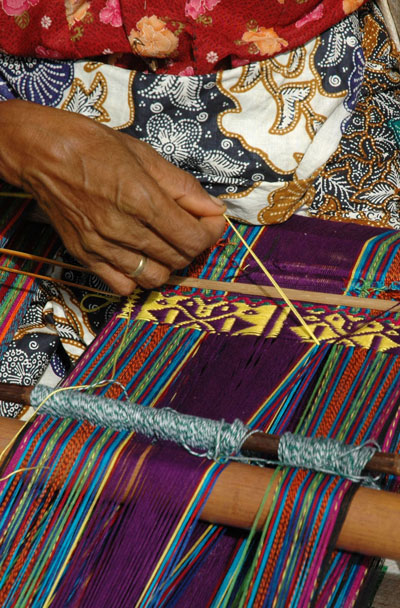
Meli-Meli
Meli-Meli is floating weft technique used extensively by LO’UD Cooperative weavers from the highlands on the southeast coast of Timor-Leste. Intricate and time-consuming, the technique requires a high level of expertise and is used to add motifs such as flowers, stars and letters during the weaving process.
Plant Dye
Raw cotton is dyed using natural pigments obtained from local leaves, bark, roots, ash, mud and clay. All weavers have their secret recipe to create desired tones, be it brown, blue, green, yellow or pink, and a good dyer is seen to be a brilliant alchemist. The process can take from two or three days to a few months depending on the complexity of the tone and the number of colours to be combined. Colours are specific to the local environment and available organic materials.
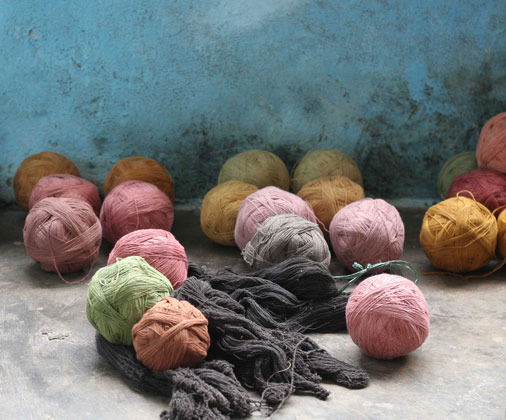
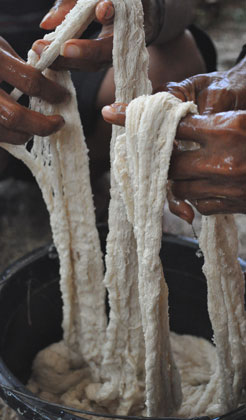
Fairly Traded
FAIR TRADE PRICING: Fair Trade makes a tangible contribution to the fight against global poverty and allows consumers to help protect the interests of producers. However other than coffee, there has been little focus on fair trade development in Timor-Leste.
In 2011, we began work with LO’UD to integrate fair trade principles into their business model and textiles production. Our research resulted in the first fair trade pricing frameworks for textiles in Timor-Leste. We also gathered information and did comparative analysis of pricing from around the country, which showed that the majority of hand-weavers were earning less than 30% of the National Minimum Wage, some earning as little as fifteen cents per hour.
The framework developed for LO’UD delivers fair incomes to Cooperative members. This significant outcome has positive implications for women all over the island.
Design Innovation
There’s always a great story behind any innovation. Both LO’UD and ETWA’s missions are to end poverty by empowering women involved in hand-crafts production. To help LO’UD members produce market-ready textiles while building on their amazing strengths as weavers, ETWA members used their expertise to develop a range of design, production and business tools. A perfect fusion! Click here to read our story.
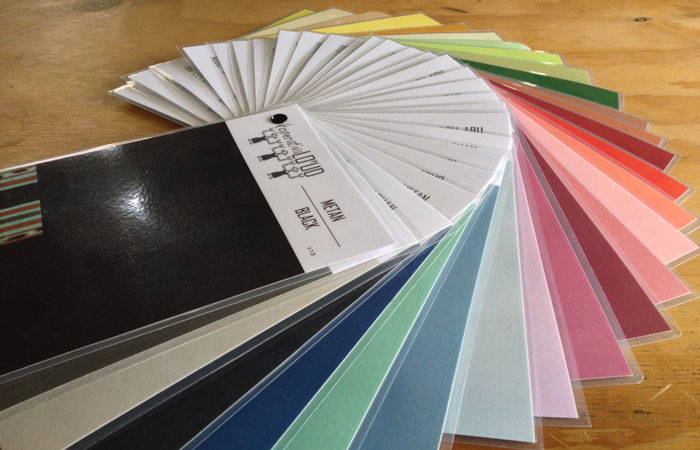
Care Instructions
Please remember all goods are plant-dyed and hand-woven by weavers in Timor-Leste. Each textile is a unique expression of the personality and creativity of each weaver, and just like the women, size and colours vary slightly, making each individual textile equally unique!
Plant Dyes
Natural plant dyes have a unique temperament and character. They are made from leaves, roots, barks and muds at the hands of master dyers.
- There may be natural variation in the finished colour of cotton within each textile and textiles within a range.
- They age in a beautiful way when kept out of direct sunlight, which can increase fading.
Wash Instructions
These textiles are best hand-washed separately with very mild, non-caustic soap in cool water. Dry flat in shade.
ETWA takes no responsibility for shrinking or fading of textiles if they are not washed or cared for following our advice.